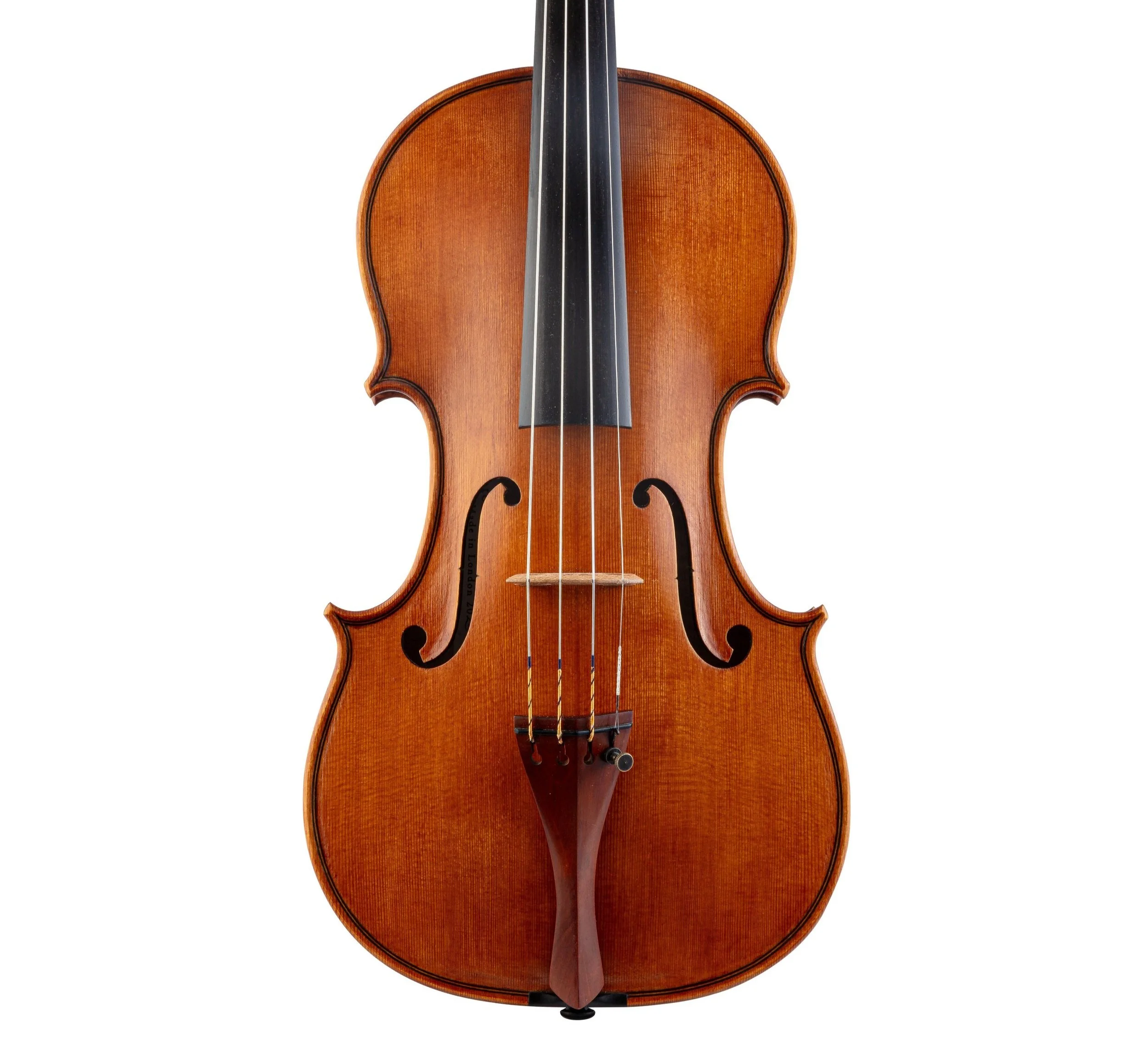
Violin Luthier
The making, restoration and maintenance of violins
We construct violins from the finest materials, carefully selecting timber from around the world.
Every violin is made using classical techniques, passed down through the centuries. Using age-old, proven methods, we create sound from the highest quality raw materials.
Using over 80 pieces of wood, a violin luthier will take 5 weeks to make each violin.
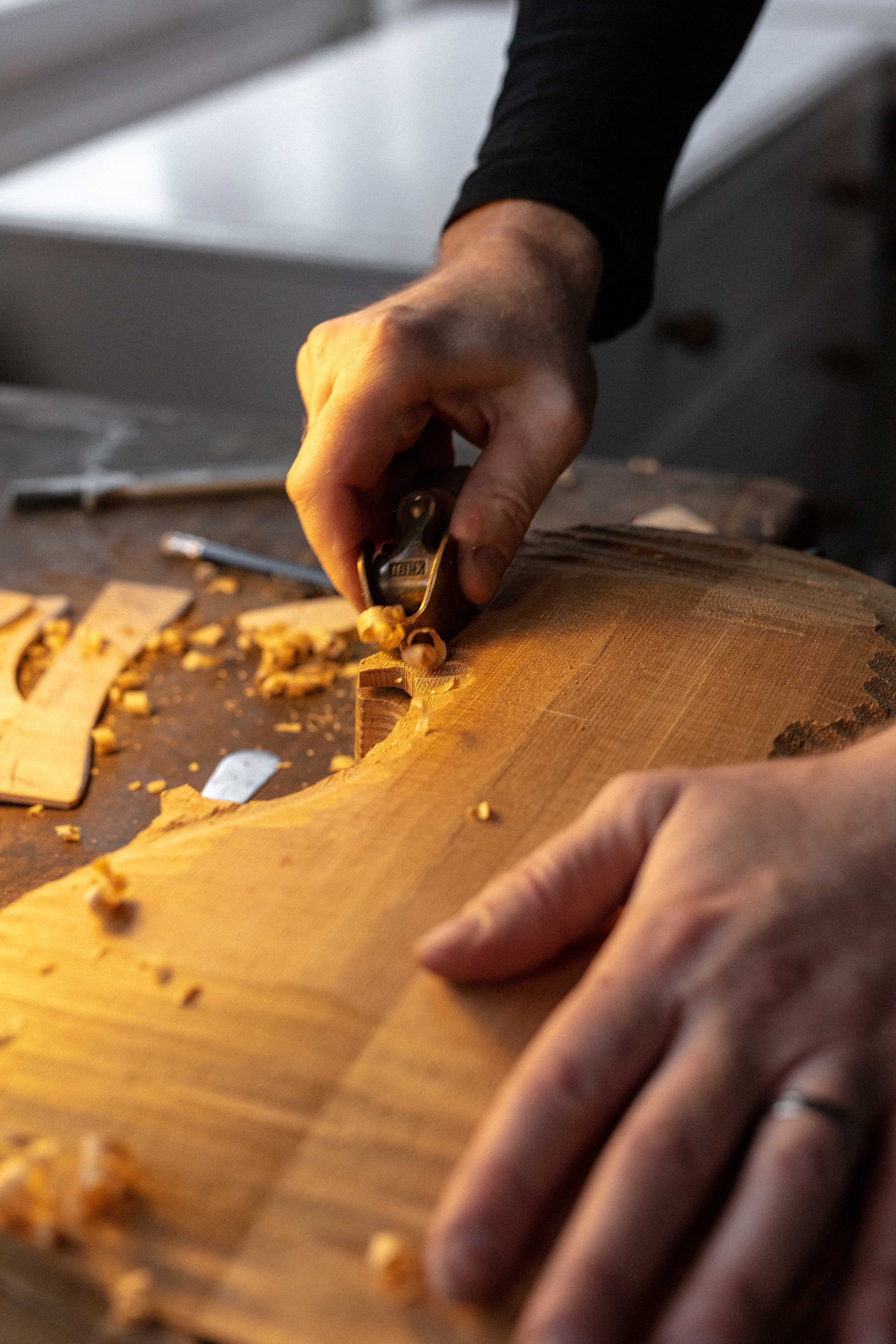
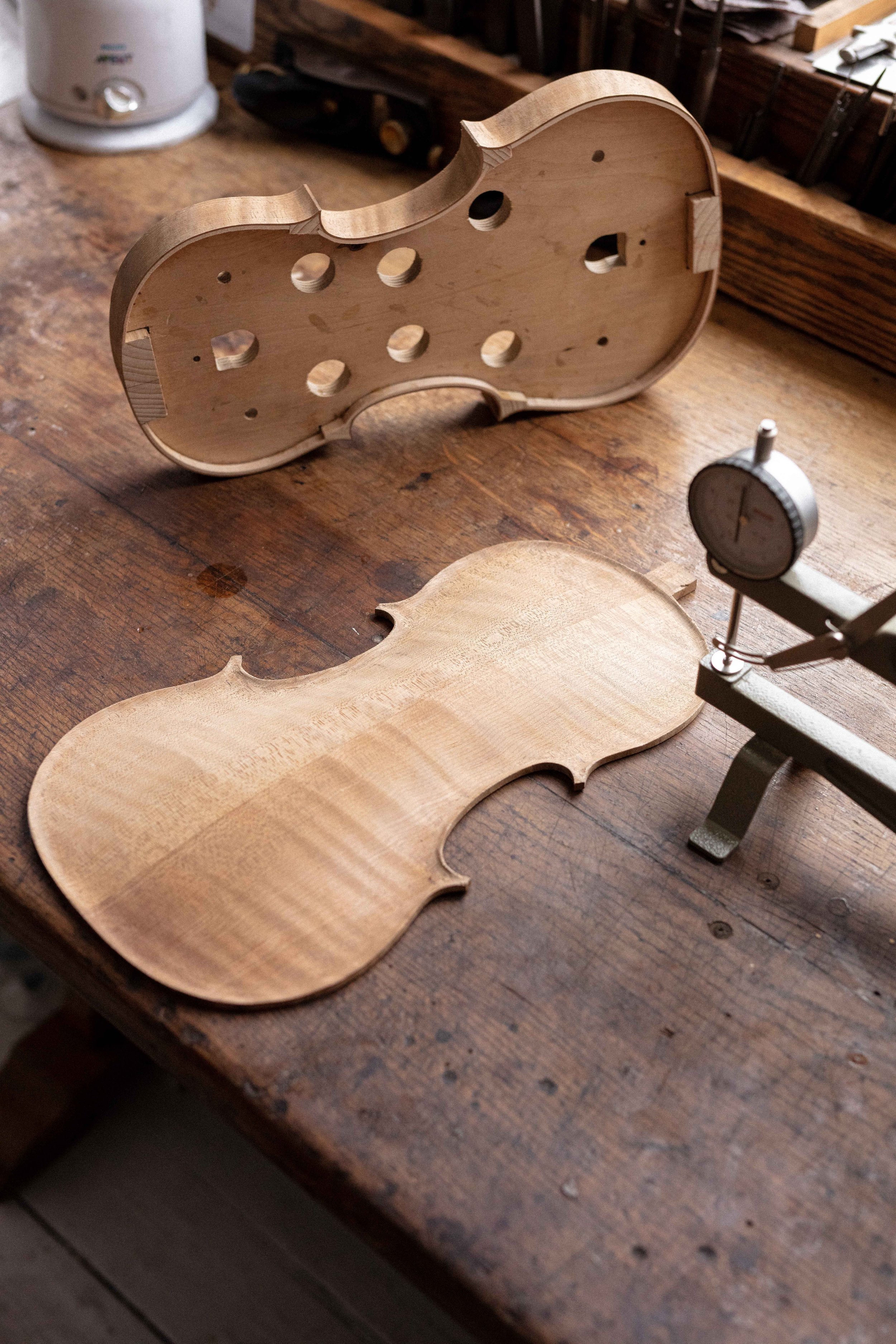
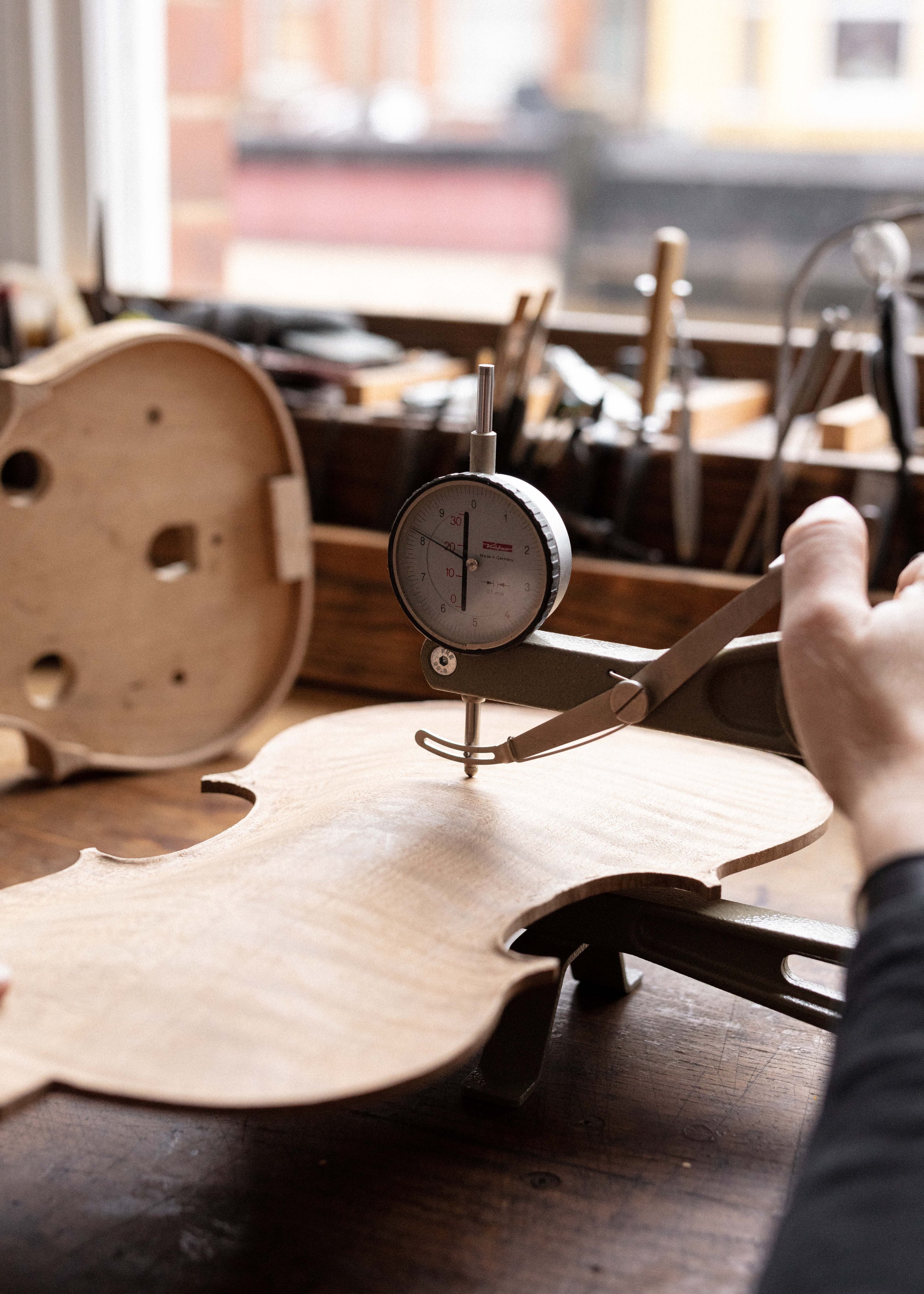
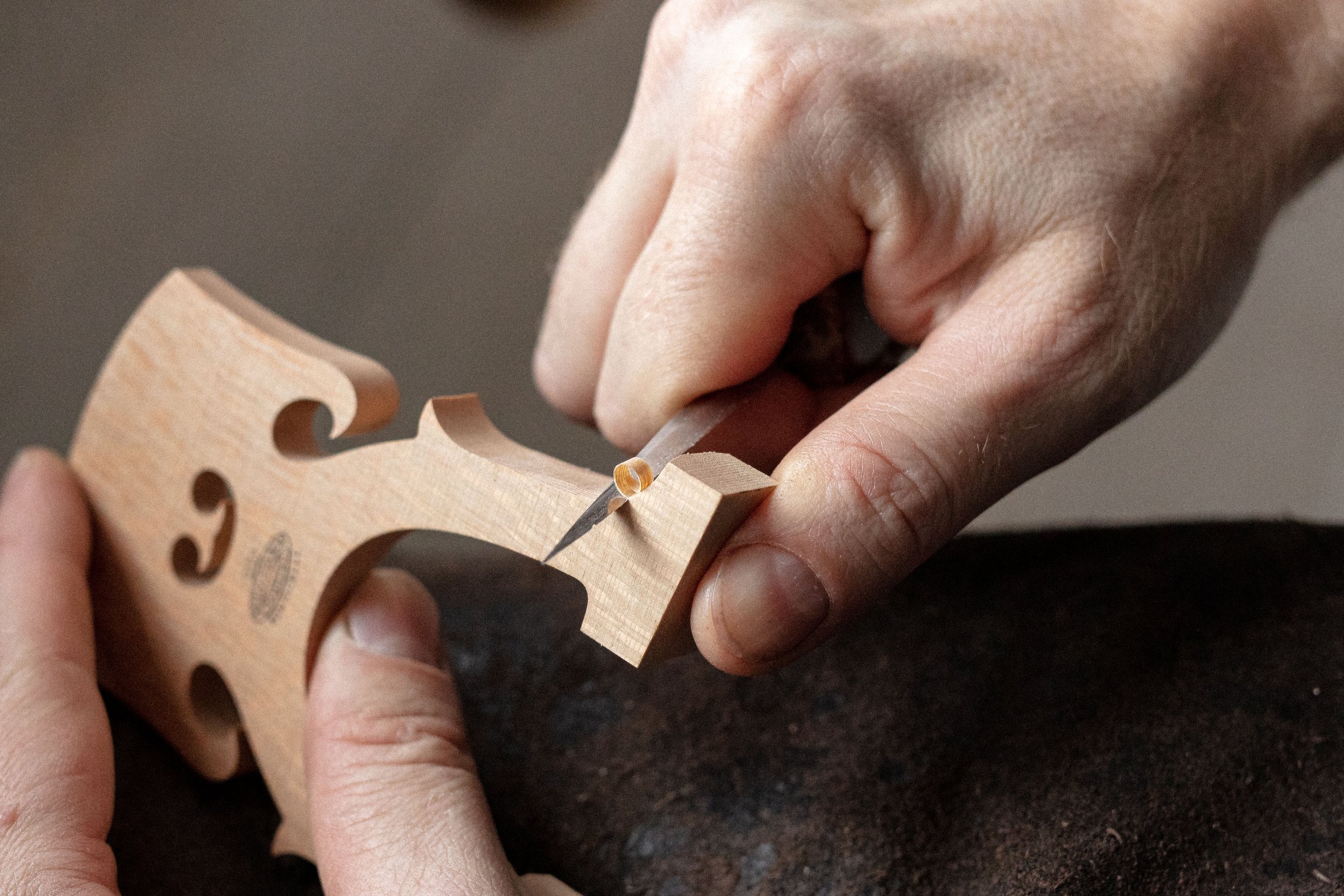
A bespoke bridge made personally for your violin will enhance the characteristics of the instrument to its full potential.
Working with you the musician, we will get the perfect playability and sound by creating a violin bridge that is just right.
Using the highest quality seasoned maple and thousands of previous success stories, we will maximise your playing.
Ruschil London bespoke violin bridges
Making a new violin top nut for a violin
Before and after shots of a new ebony violin top nut for a violin
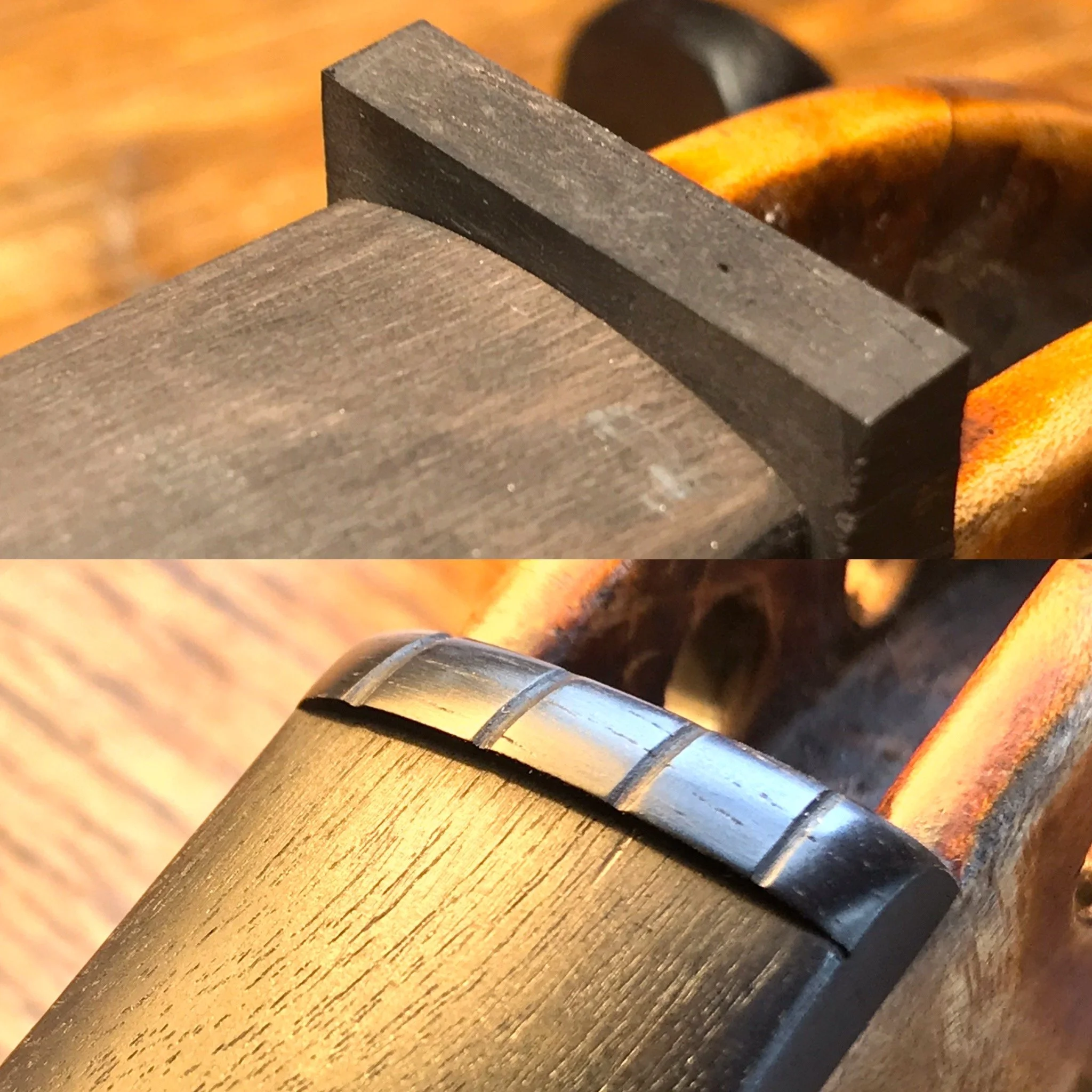
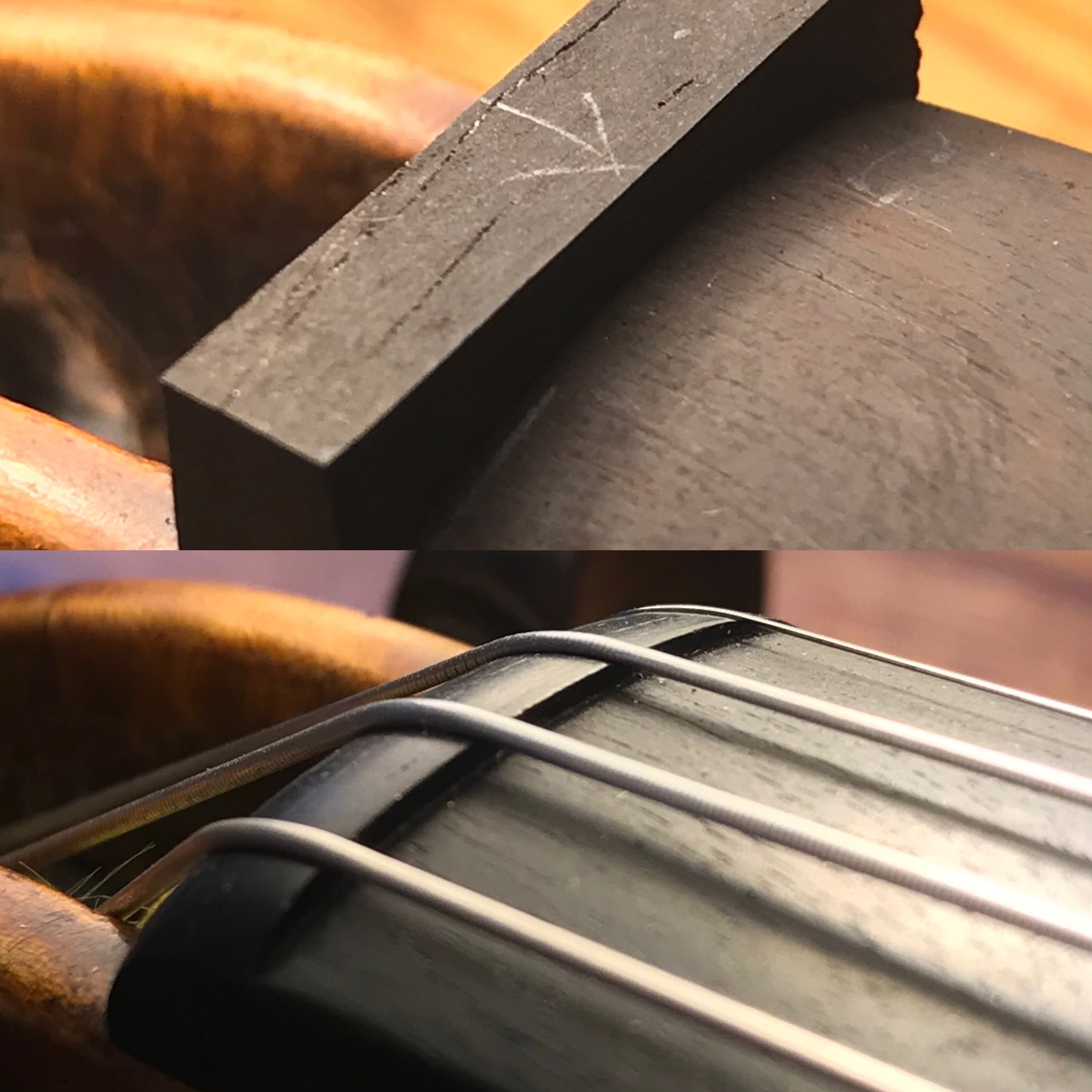

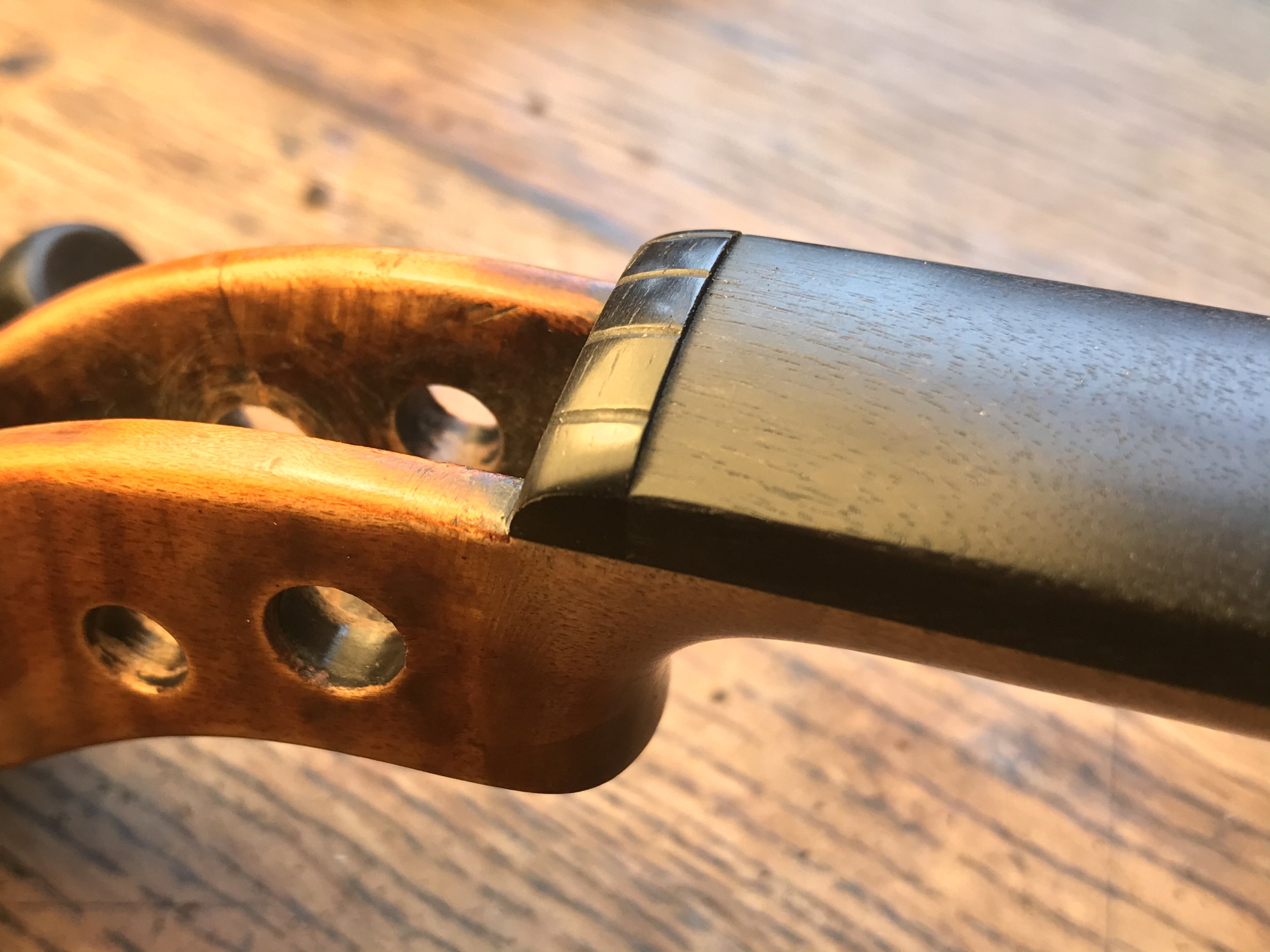
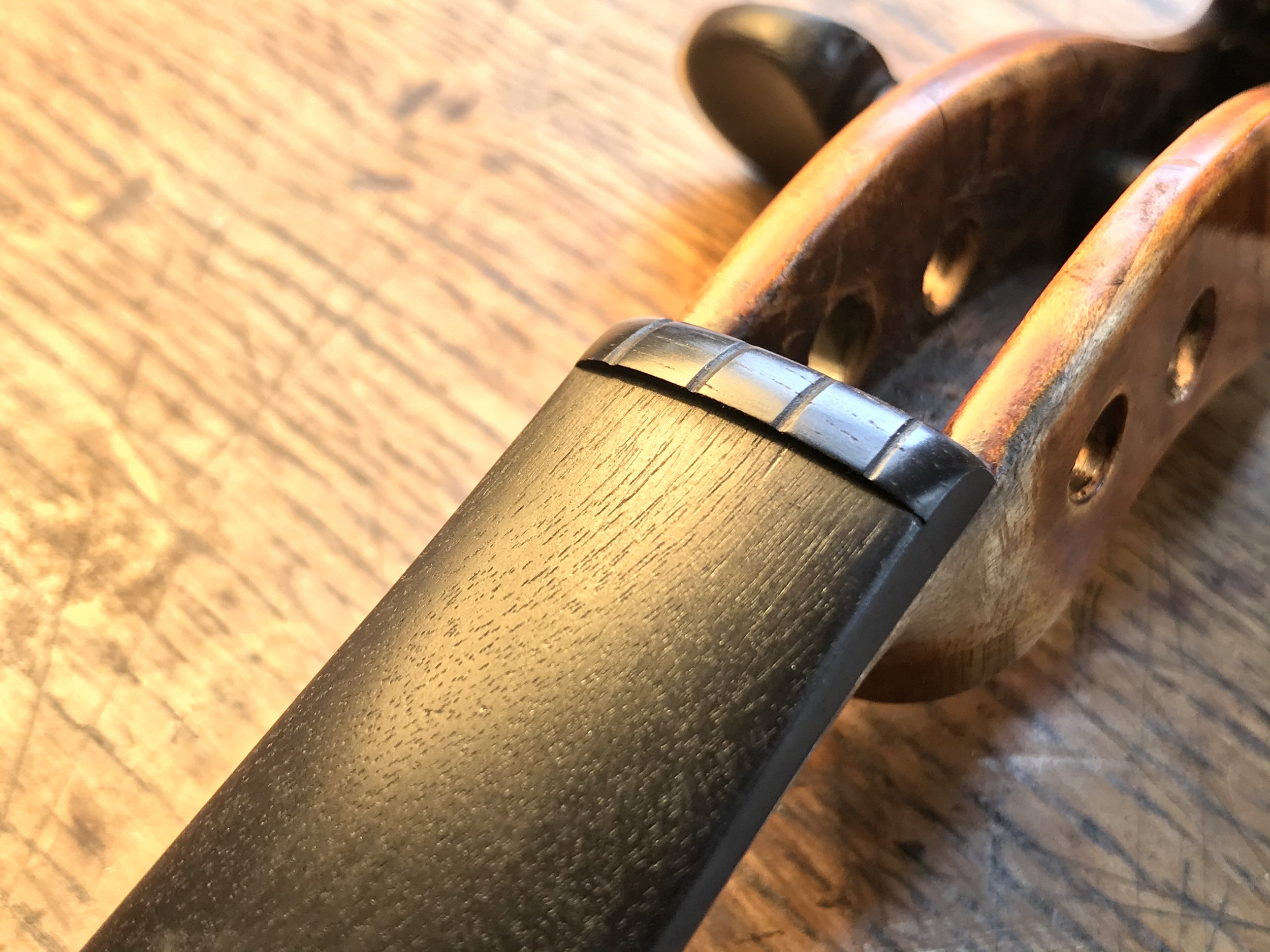
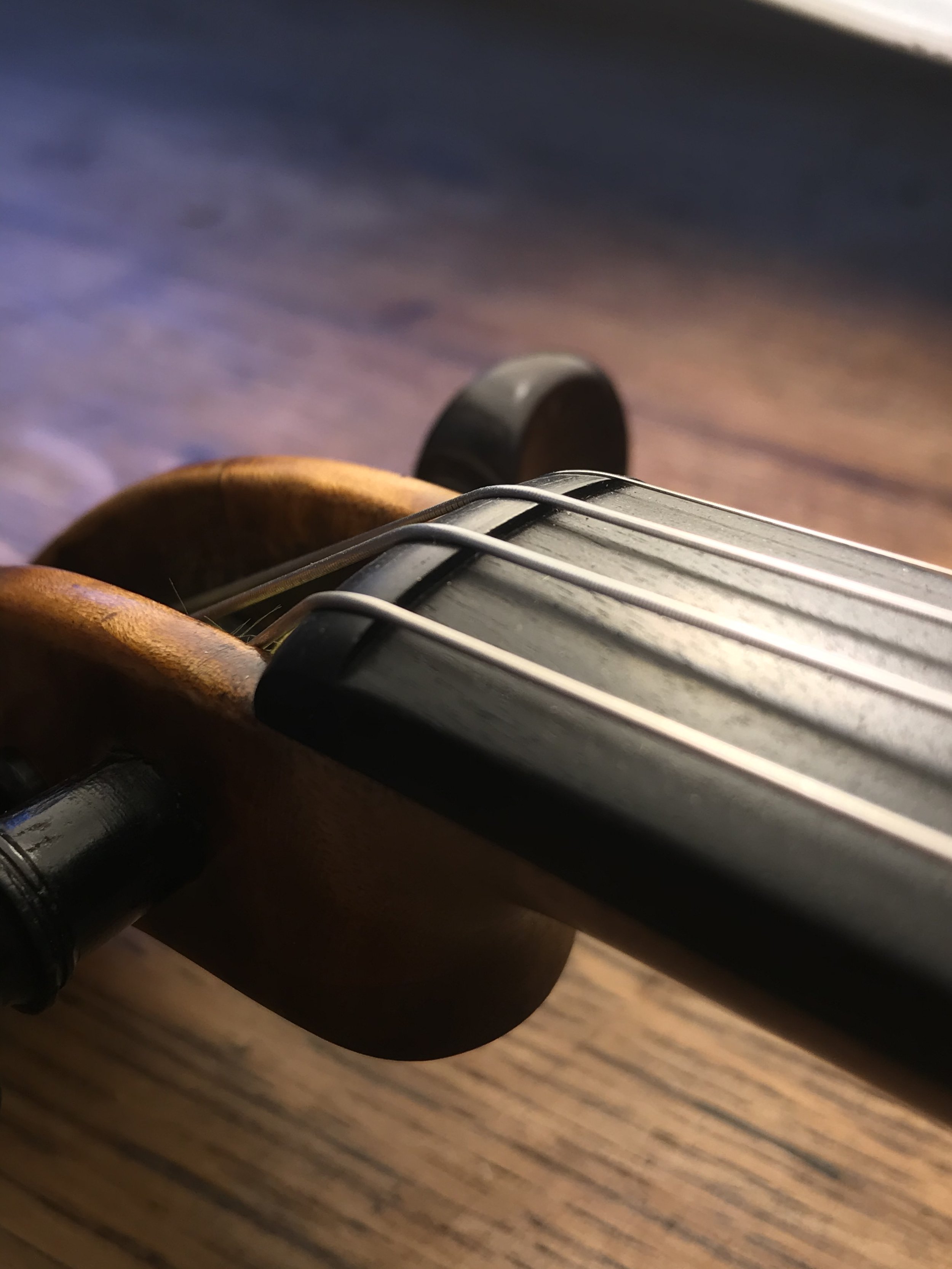
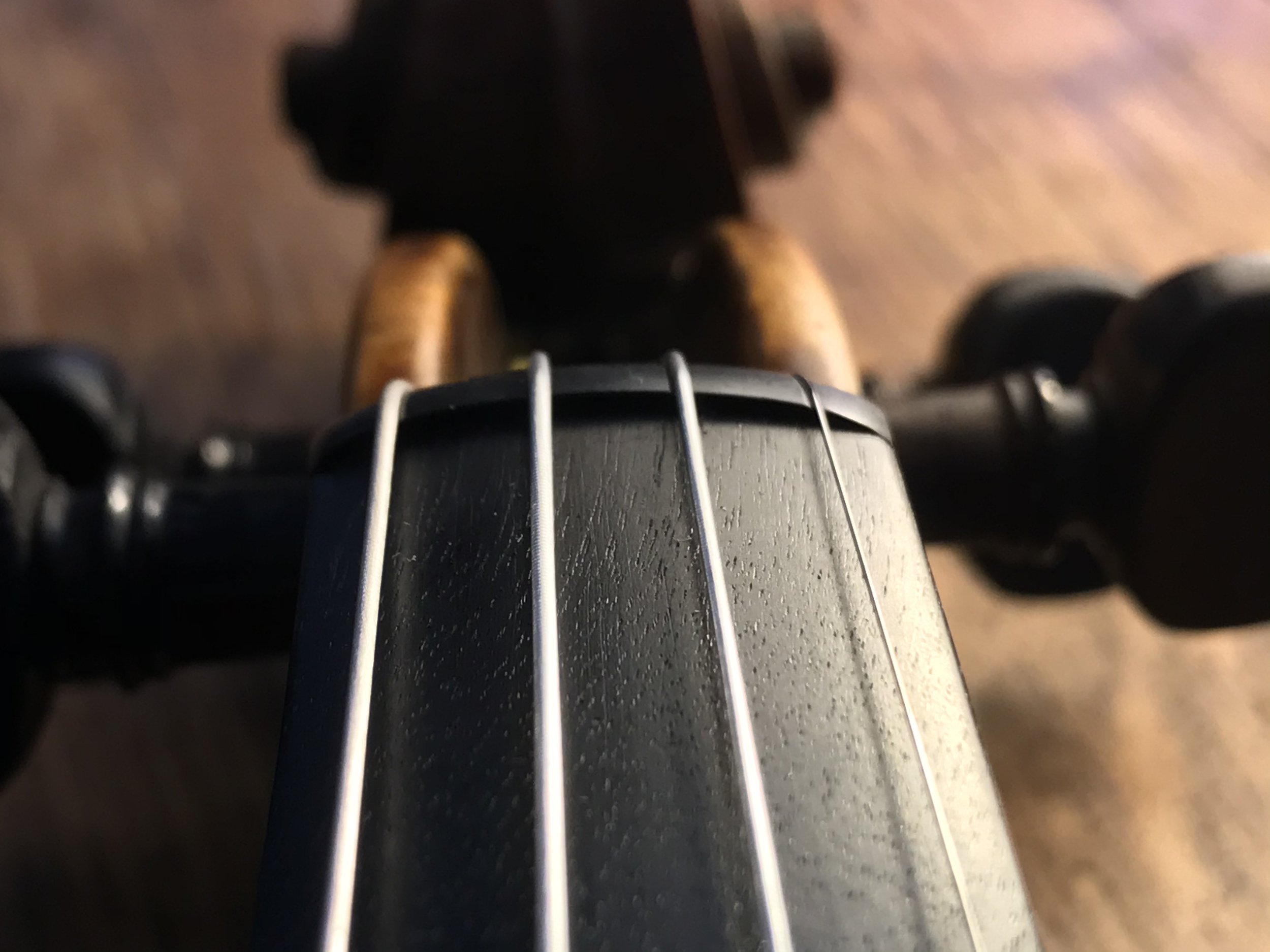
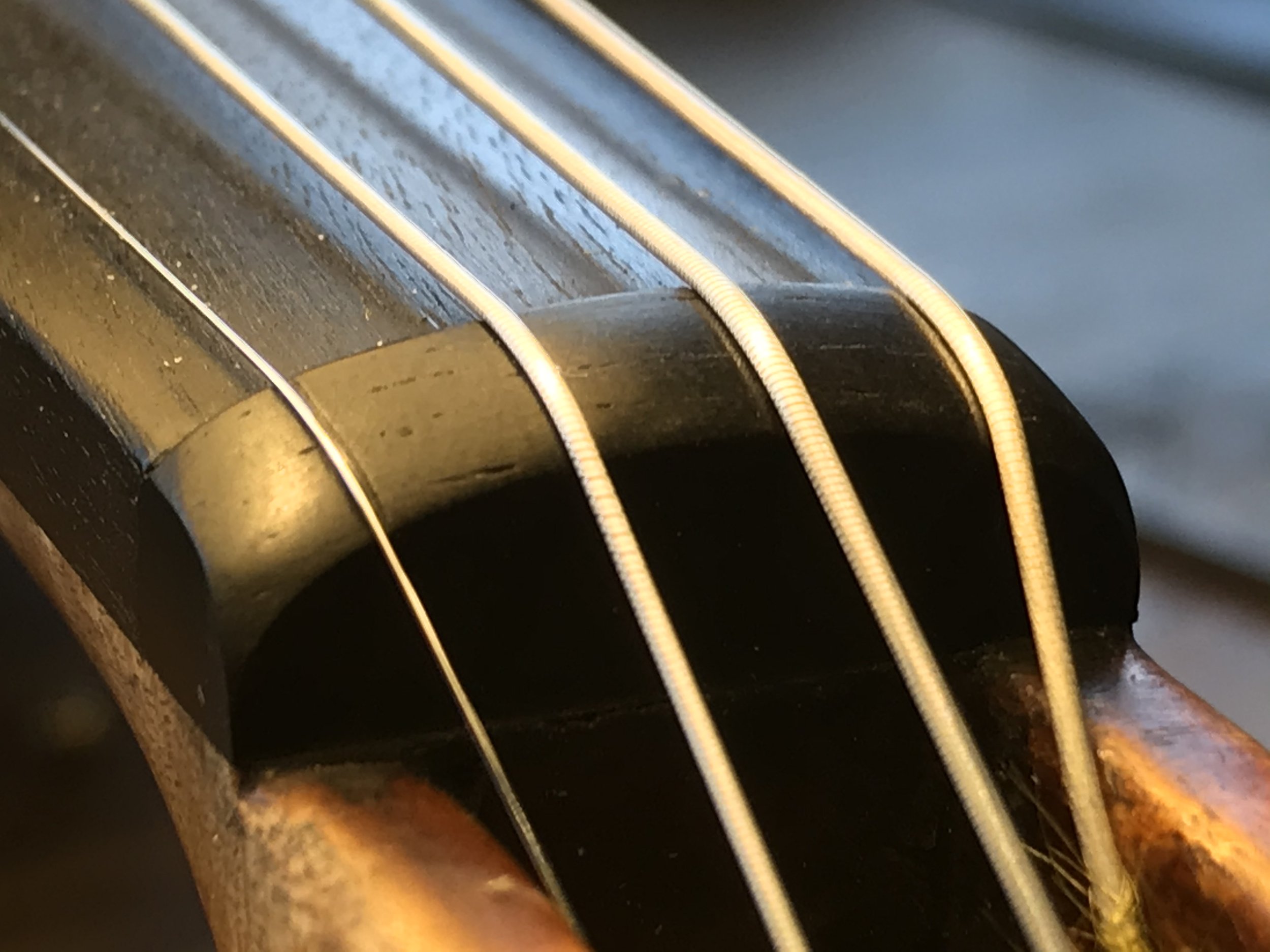
Customers are welcome to contact us using the link below, where we aim to respond to you within the hour:
Varnish Restoration on a Violin
Below is a step by step example of varnish repair from the Ruschil workshop, as explained in detail below
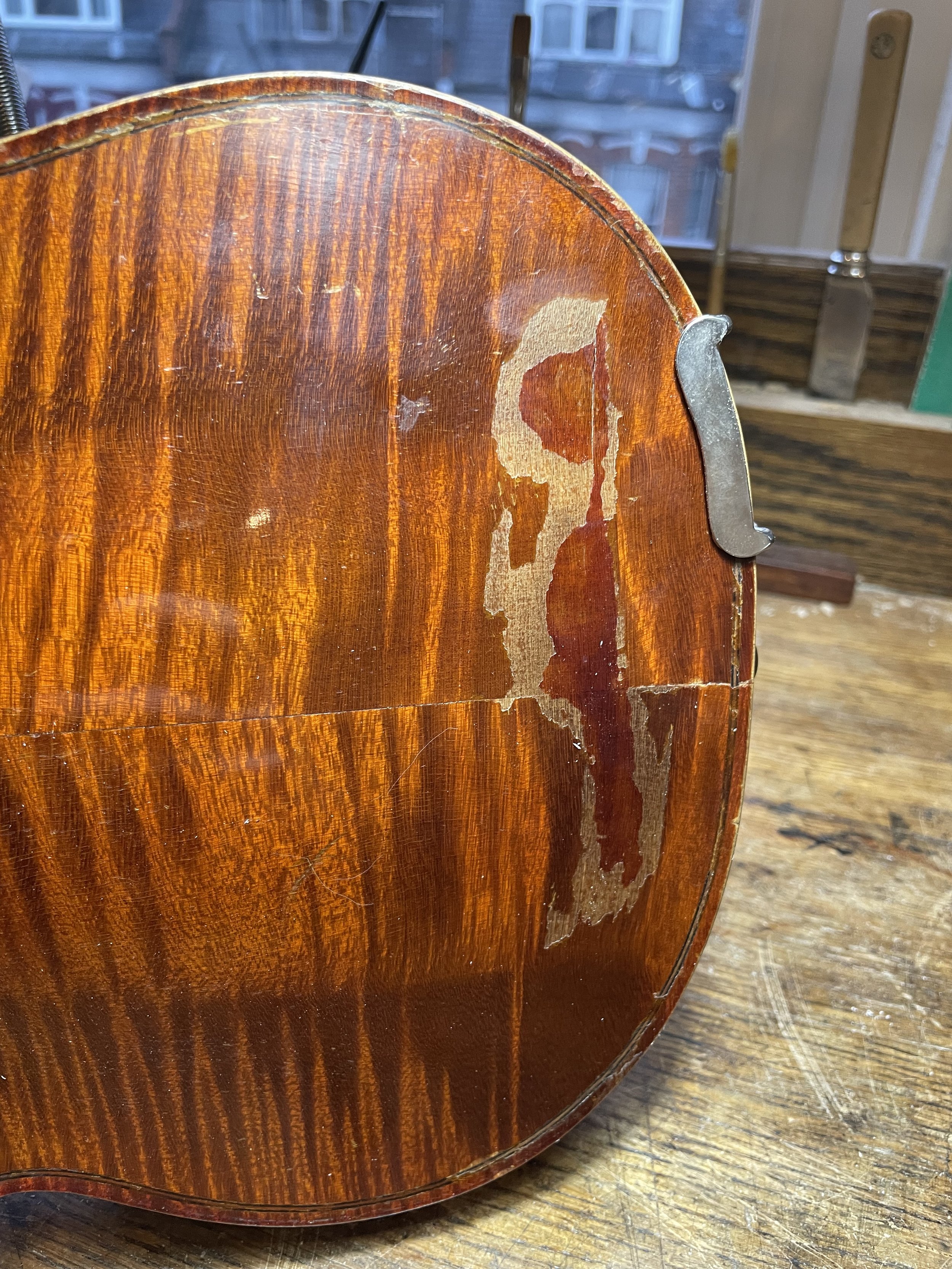
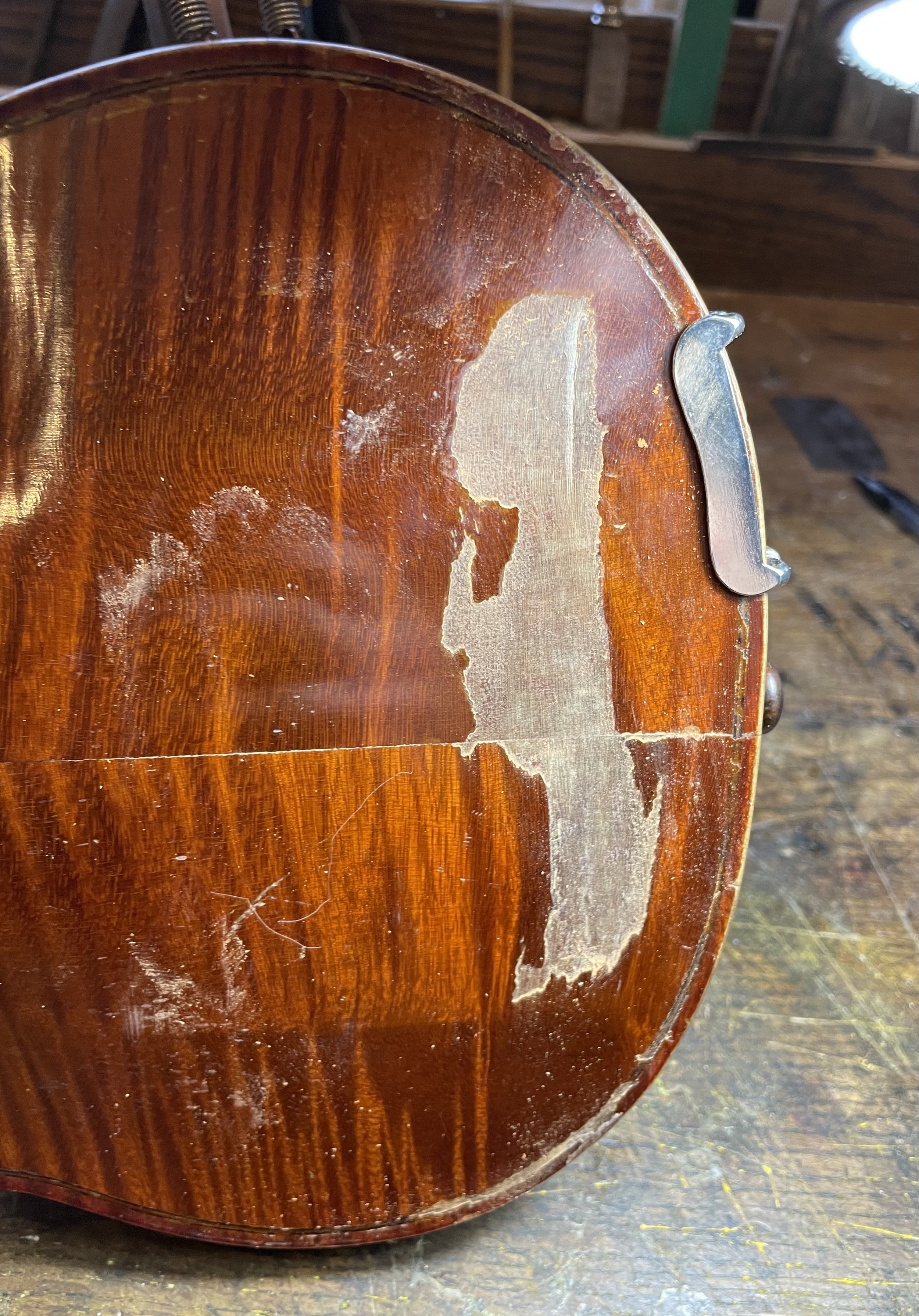
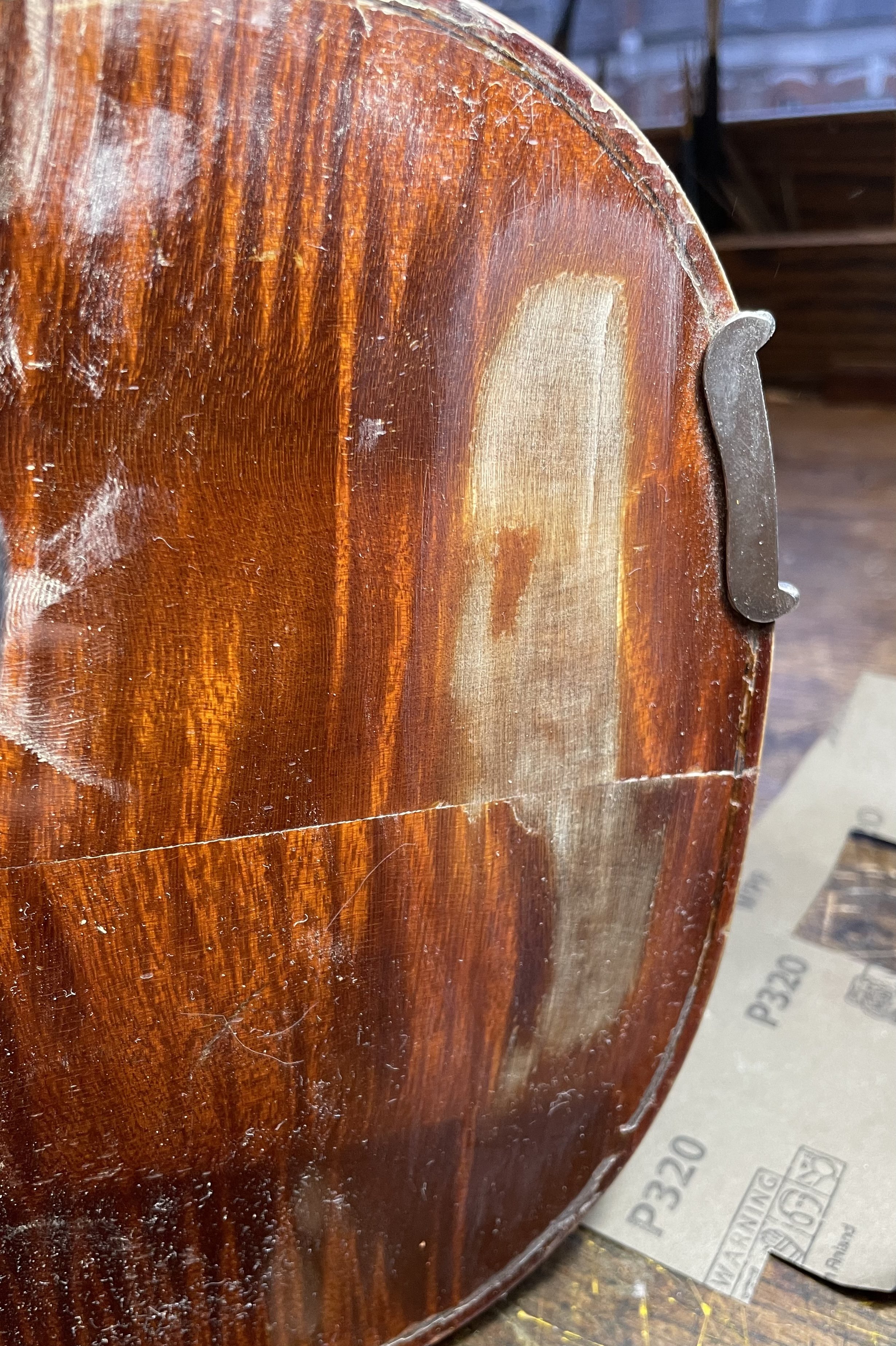
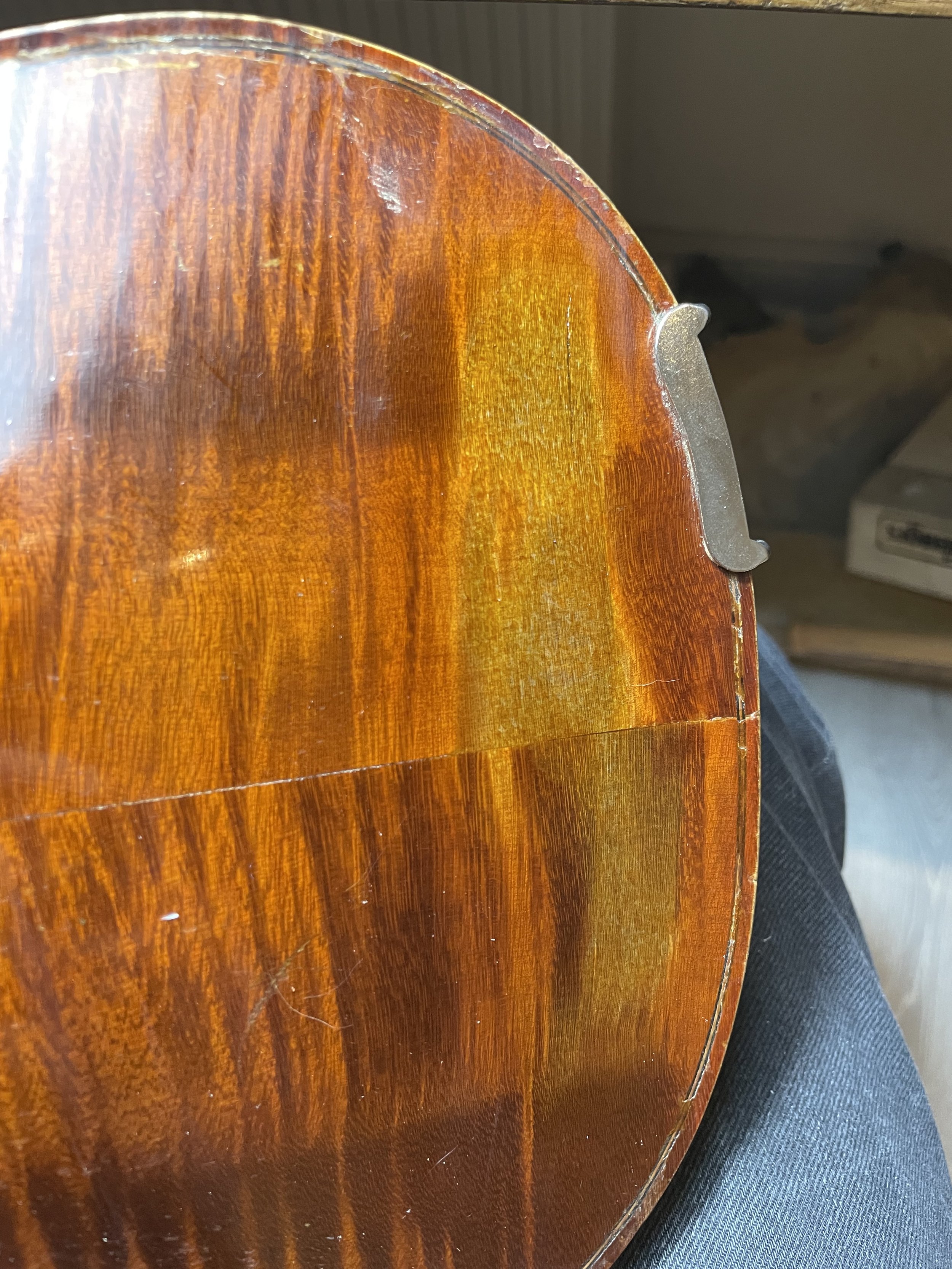
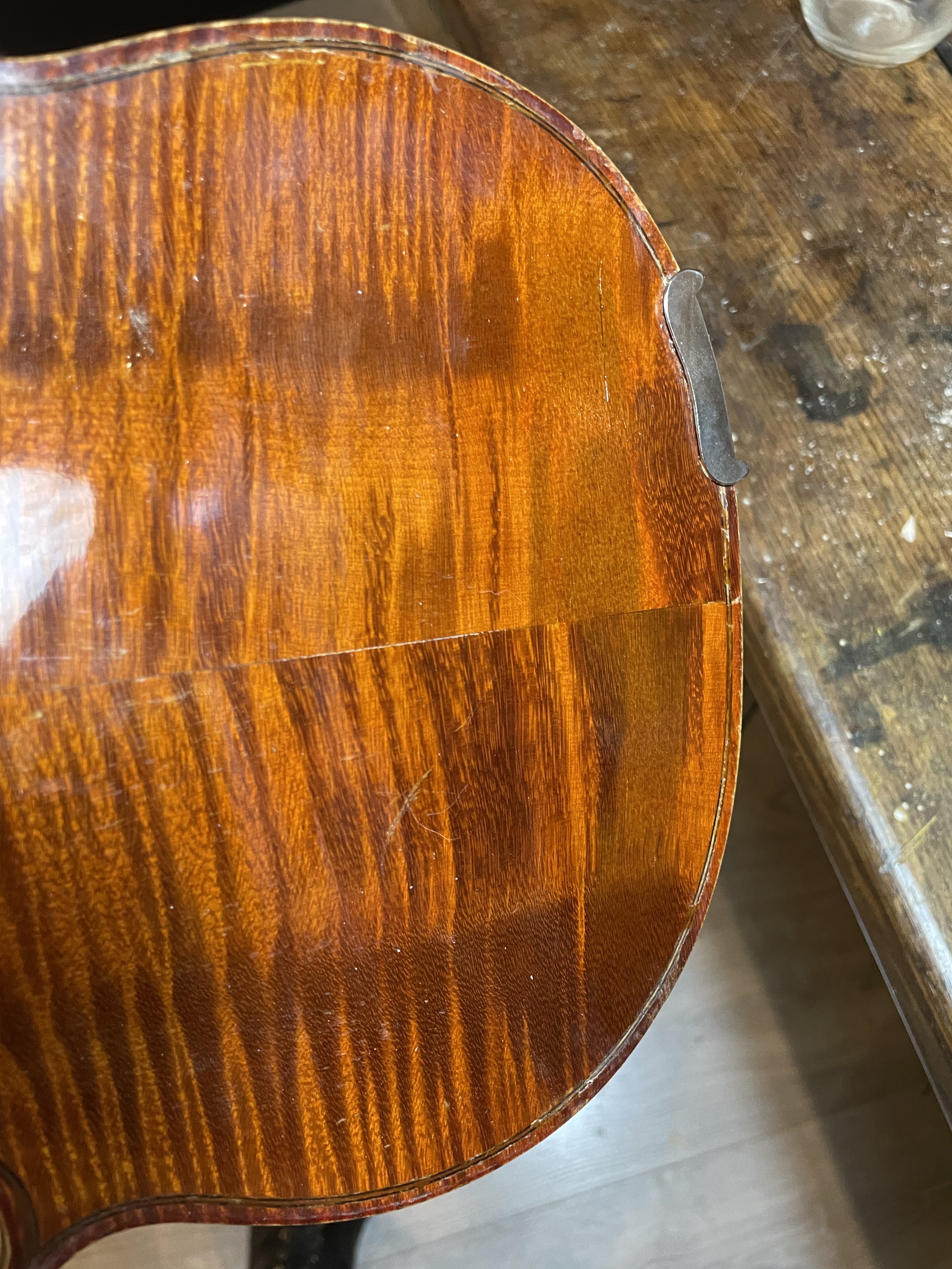
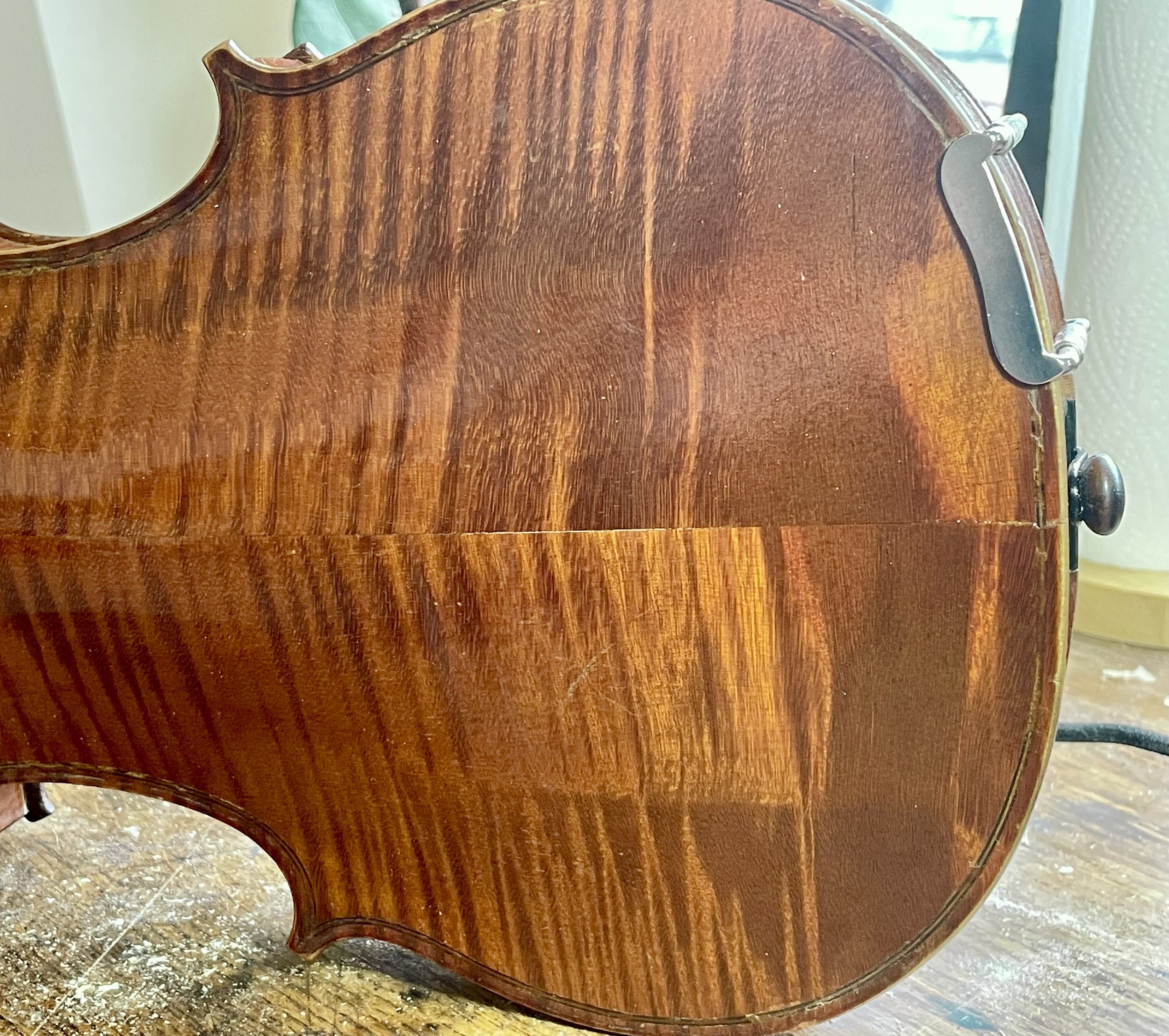
Photo 1: Assessing the damaged varnish. The original varnish of the violin has chipped off over time, right down to the bare wood. We can also see that an attempt has been made to retouch the varnish previously, leaving a red patch in the middle.
Photo 2: The previously made retouching is removed, so as to add a colour that matches the original varnish.
Photo 3: The edges are smoothed, removing the hard lines from the chipped varnish, This will make the retouching easier to blend into the original .
Photo 4: After sealing the wood with clear varnish, colour is slowly added. We start with the lightest colour, a light golden yellow, using a pointillism technique.
Photo 5: The colour varnish gets slowly redder and darker as we build up through the layers, creating depth. Between every layer, the colour is sealed and flattened with clear varnish.
Photo 6: The finished colour. From here clear varnish layers are added, cut back and flattened to create a perfect surface finish.
Violin lutherie in London
The assembly of violin parts during the construction of a new violin at the London atelier. Traditional lutherie involves over seventy pieces of wood of different species being carefully crafted and beautifully put together
Crafting Harmonies: The Art and Passion of Being a Violin Luthier
In the realm where artistry meets craftsmanship, being a violin luthier is a calling that requires a delicate touch, an acute ear, and a profound love for the soul-stirring melodies that emanate from the delicate strings of a violin. Beyond the workshop tools and wood, being a violin luthier is an art, a journey, and a commitment to preserving and enhancing one of the most revered instruments in the world of classical music.
The Artistic Journey Begins: The path of a violin luthier starts with an early fascination for the instrument's intricate design and the captivating music it produces. This journey involves a deep connection to the heritage of violin-making, studying the time-honoured techniques passed down through generations. From selecting the finest tonewoods to understanding the complex acoustics, the luthier's artistic journey begins with an appreciation for every nuance of the instrument.
Wood, Craft, and Precision: The heart of a violin lies in the wood that forms its body. As a violin luthier, the process involves meticulously carving and shaping the spruce and maple to create the top and back plates, carefully considering every contour. The scroll, the f-holes, and the delicate purfling are crafted with precision, a dance of hands that brings the instrument to life. Each instrument is a unique creation, with the luthier's signature embedded in every detail.
Striking the Perfect Chord: Crafting a violin is not just about aesthetics; it's about coaxing the perfect sound from the instrument. The luthier must navigate the delicate balance of plate thickness, arching, and varnishing to achieve a harmonious balance of warmth, projection, and responsiveness. It's a pursuit of the elusive combination that makes a violin not just an instrument but a partner in the hands of a musician.
Varnishing as an Art Form: The final stages of violin-making involve applying varnish, a step that imparts character and protection to the instrument. The choice of varnish, the application technique, and the drying process all contribute to the final aesthetic and tonal qualities of the violin. A skilled luthier understands the interplay of varnish with the wood, creating an instrument that not only sounds beautiful but also possesses a visual allure.
Collaboration with Musicians: The journey of a violin luthier extends beyond the workshop and into collaboration with musicians. Understanding the preferences, playing styles, and tonal aspirations of violinists becomes a crucial aspect of the craft. The feedback from musicians shapes the luthier's approach, leading to instruments that resonate with the unique needs of the players.
Legacy and Continuity: Being a violin luthier is not merely a profession; it is a contribution to the legacy of classical music. Each violin crafted is a link in a chain that stretches back through time, connecting with the great luthiers of the past. The continuity of tradition and the innovation brought by contemporary luthiers contribute to the evolving narrative of violin-making.
In the hands of a skilled violin luthier, a piece of wood becomes a vessel for the symphony of centuries. It transforms into an instrument that not only resonates with the skill and dedication of its creator but also carries the potential to stir the deepest emotions. Beyond the craftsmanship, being a violin luthier is a journey of passion, creativity, and a commitment to perpetuating the enchanting legacy of the violin.
